Compressed air filters are essential components in various industrial and manufacturing processes. They play a crucial role in ensuring the quality of the air supply by removing contaminants, moisture, and particulates. However, despite their importance, many users make critical mistakes when operating these filters. In this article, we’ll explore the top mistakes people make when using compressed air filter and how to avoid them for optimal performance.
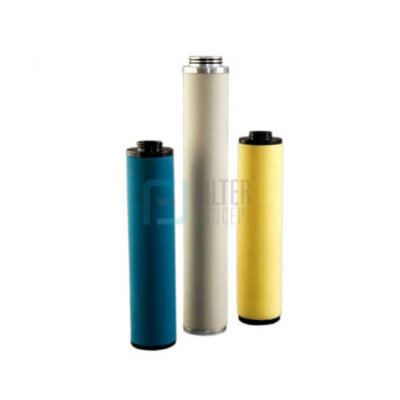
Understanding Compressed Air Filters
Before diving into the common mistakes, it’s vital to understand what compressed air filters are and why they matter. Compressed air filters are designed to purify the air before it enters pneumatic tools and equipment. They typically remove particles, oil, and moisture, which can cause damage and reduce efficiency.
The Importance of Proper Filtration
Using unfiltered or poorly filtered air can lead to numerous problems, including equipment failure, decreased efficiency, and increased costs due to repairs and maintenance. A well-maintained air filtration system not only protects your equipment but also ensures a safer working environment.
Mistake #1: Neglecting Regular Maintenance
One of the most significant errors users make is neglecting regular maintenance of their compressed air filters. Filters need to be cleaned and replaced regularly to ensure they function effectively. Failure to do so can result in:
- Increased pressure drop: Clogged filters can lead to reduced airflow.
- Higher energy costs: Inefficient filters force compressors to work harder.
- Shortened equipment lifespan: Contaminants can damage sensitive components.
Solution: Establish a Maintenance Schedule
Implementing a routine maintenance schedule will help ensure your filters operate optimally. Check the manufacturer’s recommendations for filter replacement and adhere to those guidelines.
Mistake #2: Choosing the Wrong Filter Type
Not all compressed air filters are created equal. Many users make the mistake of choosing the wrong type of filter for their specific application. Factors to consider include:
- Air quality requirements: Some applications need cleaner air than others.
- Filter size: Ensure the filter is appropriately sized for your system.
- Flow rate: The filter should match the airflow demands of your tools and equipment.
Solution: Assess Your Needs
Evaluate your air quality requirements and consult with a filtration expert if necessary. This step can save you from costly mistakes in the future.
Mistake #3: Overlooking System Design
Another common mistake is overlooking the overall design of the compressed air system. An improperly designed system can lead to inadequate filtration, resulting in contaminants reaching your equipment.
Key Considerations:
- Pipe sizing: Ensure pipes are adequately sized to prevent pressure drops.
- Filter placement: Filters should be placed strategically within the system to maximize efficiency.
- Air storage: Properly designed air receivers can help reduce moisture accumulation.
Solution: Design with Efficiency in Mind
Work with a professional to design or evaluate your compressed air system. A well-planned setup will help maintain clean air and optimize filter performance.
Mistake #4: Ignoring Ambient Conditions
Ambient conditions can significantly impact the performance of compressed air filters. Factors such as temperature, humidity, and dust levels can affect how filters operate.
Impact of Ambient Conditions:
- High humidity: Can lead to increased moisture in the air supply, overwhelming filters.
- High dust levels: Can clog filters quickly, necessitating more frequent changes.
Solution: Monitor and Adjust
Regularly monitor the ambient conditions in your facility. Adjust your filtration system as necessary to accommodate changes in the environment.
Mistake #5: Inadequate Training for Operators
An often-overlooked mistake is inadequate training for operators using compressed air systems. Without proper training, operators may not understand how to effectively use and maintain filters.
Common Training Gaps:
- Understanding pressure settings: Incorrect settings can lead to filter damage.
- Recognizing signs of contamination: Operators should be trained to spot issues early.
- Knowing maintenance protocols: Proper procedures can help extend filter life.
Solution: Invest in Operator Training
Provide comprehensive training for all personnel involved with the compressed air system. Regular training updates will help ensure everyone is up-to-date on best practices.
Mistake #6: Failing to Monitor Filter Performance
Another significant error is failing to monitor filter performance. Just because a filter appears clean does not mean it is functioning correctly.
Signs of Poor Performance:
- Increased energy consumption: Can indicate filter blockage.
- Unusual noises from compressors: May signal airflow issues.
- Frequent equipment malfunctions: Can suggest contaminants are getting through.
Solution: Implement Monitoring Tools
Utilize pressure gauges and other monitoring tools to keep an eye on filter performance. Regular checks will help you catch issues before they become significant problems.
Mistake #7: Underestimating Moisture Management
Moisture can wreak havoc on compressed air systems. Underestimating moisture management is a common mistake that can lead to:
- Corrosion of tools and equipment
- Reduced air quality
- Increased maintenance costs
Solution: Use Moisture Separators
Incorporate moisture separators and drains into your compressed air system. These tools help remove moisture before it reaches your filters and equipment.
Mistake #8: Using Low-Quality Filters
Choosing low-quality filters to save costs is a frequent error. While it may seem like a good idea at the moment, using inferior filters can lead to more significant issues down the line.
Consequences of Low-Quality Filters:
- Higher risk of failure: Cheap filters may not withstand the demands of your system.
- Increased contaminants: Poor filtration leads to more contaminants in the air.
- Shorter lifespan for equipment: Protecting your tools is worth the investment.
Solution: Invest in Quality Filters
While it might be tempting to cut corners, investing in high-quality filters is crucial. Consider reputable brands that offer reliable performance and durability.
Mistake #9: Ignoring Filter Specifications
Each filter comes with specific specifications that need to be followed. Ignoring these can lead to inadequate filtration and potential equipment damage.
Key Specifications to Follow:
- Maximum operating pressure: Exceeding this can lead to catastrophic failure.
- Temperature ratings: Ensure filters can handle the temperature of your application.
- Flow capacity: Use filters that meet the flow requirements of your system.
Solution: Review Specifications Regularly
Always consult the filter’s specifications before installation and maintenance. Adhering to these guidelines will help maintain optimal performance.
Mistake #10: Lack of Documentation
Finally, many users fail to maintain proper documentation of their compressed air systems. Without records of maintenance and filter changes, it can be challenging to track performance and identify issues.
Importance of Documentation:
- Historical data: Helps identify trends and recurring problems.
- Maintenance schedules: Keeps track of when filters need to be changed.
- Regulatory compliance: Ensures you meet industry standards and regulations.
Solution: Keep Detailed Records
Implement a system for documenting all maintenance activities, filter changes, and performance metrics. This practice will aid in troubleshooting and ensure compliance with industry standards.
Conclusion
In summary, understanding and avoiding the top mistakes people make when using compressed air filters can lead to better system performance, lower costs, and increased equipment lifespan. By focusing on regular maintenance, proper filter selection, operator training, and thorough documentation, you can ensure that your compressed air system runs efficiently and effectively. Taking these steps not only protects your equipment but also contributes to a more productive working environment. Remember, investing time and resources into your compressed air filtration system is an investment in the overall health of your operations. read more….
Leave a comment
Your email address will not be published. Required fields are marked *